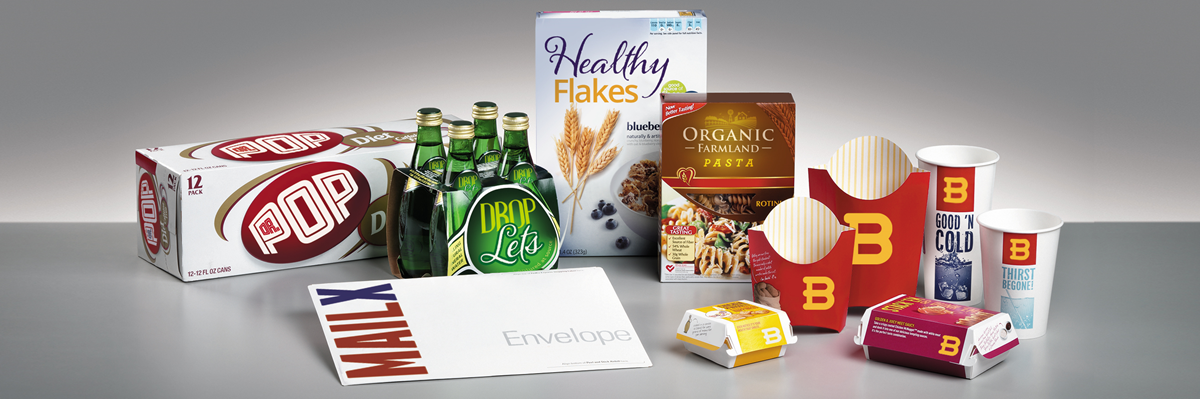
Less Waste, Higher Speed, Fewer Logistics, Fewer Personnel: Flexible Web-Fed Platen Die-Cutting Solutions for Folding Carton Production
Original Article was reprinted from the March 2021 issue of Folding Carton Industry magazine
With its brand Zerand, BW Papersystems, a leading manufacturer of high-speed web-fed platen die-cutting machinery, offers a real alternative to conventional sheet-fed folding carton production. Their web-fed platen die-cutting solutions allow for flexible production and line configurations suitable for every concept of operating environment.
For years, folding carton producers have been facing an aggressive price point set by the industries they serve. In response, they are continuously searching for real solutions to the challenges they face: Reduction of material, logistics and personal costs. Conventional production processes where reels are converted into sheets which are then printed on a sheet-fed press are part of the problem. They cause expensive board waste, they are personnel-intensive and demand high logistics effort.
With its Zerand web-fed platen die-cutting solutions, BW Papersystems offers a true alternative for maximum flexibility regarding production and line configuration. Being part of BW Papersystems and the Barry-Wehmiller group since September 2017, the flexible Zerand production system enables die-cutting in-line with the press for production in one operation, or offline where one press can feed more tha n one platen die-cutter with rolls of pre-printed material. The Zerand web-fed platen die-cutting solutions can run multiple short and medium runs and handle a wide range of carton types with fast job change times.
“When we talk to converters about web-fed production, they are often surprised to learn how far the technology has progressed,” explained Luigi Pessarelli, VP of Sales North America White Paper at BW Papersystems. “Many of their carton types can be produced far more efficiently than they are today using sheet-fed production.”
Both the in-line and the offline solution have their customer individual advantages and offer different efficiencies. While the in-line configuration reduces logistics and handling efforts as well as WIP of printed rolls, the offline solution can reduce the cost of automation. Opposed to having a complex and expensive robotic palletizer, folding-carton printers can connect the output of a stacker to the folder gluers by means of conveyors. Beyond that, the offline solution allows the press to run at higher speed in a roll-to-roll configuration and feed more than one platen die-cutter with rolls of pre-printed material.
In the in-line configuration, a platen cutting system works well with any type of web press, including Flexo, Offset, Gravure or Digital. “The speed and quality advances made by leading Flexo press manufacturers has seen Flexo print becoming the preferred web printing technology in the folding carton industry, previously dominated by Offset or Gravure printing,” stated Luigi Pessarelli.
A Zerand platen cutter installed in-line with a press has a capacity of 25,000 sheets per hour with widths up to 1400 mm. The entire line including a mechanized palletizing system can operate with three to four operators. Because the carton blanks are produced in one operation, floor space, waste, WIP and logistics are substantially reduced.
In any configuration, be it in-line or offline, the Zerand web-fed platen die-cutting solutions require no gripper margin and offer better carton nesting flexibility than sheet-fed dies, the board usage per carton is always lower and sometimes substantially so. A decisive criterion, as a Zerand customer who has both sheet-fed and web-fed capability in the same plant, reported,” The decision to produce a job in sheet form or web form is based mainly on the board waste. As up to 50 percent of carton blanks cost comes from the board, any saving due to web fed production is more than welcome. Reduced board usage also contributes to our environmental policy.”
In addition, web-fed platen die-cutting does not suffer the very high tooling cost associated with rotary die-cutting. In fact, tooling costs are very similar to those of a sheet-fed die-cutter.
Some other benefits of web production include the ability to apply grease or moisture barrier coatings in-line, to reverse print with no loss of production efficiency and to apply a wide range of spot and full coverage varnishes without a loss of production efficiency.
Not all Zerand customers demand wide-width solutions. Using narrower machines below 600 mm some can achieve job changes including the press in fifteen minutes and still enjoy single pass, low waste production with reduced labor costs.
In order to optimize folding-carton production, Zerand not only have an eye on the system, as Luigi Pessarelli commented, “In many meetings we initially are not talking about a machine. Instead we are talking about a production system, and what it can offer that particular site.” Customers are invited to provide details of their most common carton designs with the layout they currently use. These are studied and a report is prepared including details such as production rate and board usage per carton. “This often stimulates interest and leads to further discussions where other savings in the area of labor cost, floor space, and WIP are quantified,” explained Pessarelli. Only at this point when the process benefits are established, can the machine details be discussed.
Zerand customers run their machines at high speed, 24 hours per day, 7 days per week. To excel in the environment the machine must be both simple to operate and heavily constructed. As the machinery is so robust, critical machine sections can be rebuilt and upgraded with the latest controls and safety technology, thus, guaranteeing the protection of the customers investment over an extended period of time.
When things do go wrong, customers require urgent support and spare parts. BW Papersystems as a large group with an international service support team and regional spare parts warehouses offers worldwide support for Zerand web-fed platen die-cutters.
“The range of cartons produced by our customers is ever growing,” said Luigi Pessarelli. Common applications include cartons for fast food, beverage, mailers, pizza, cereal, tissues, toothpaste, detergent and many more. Many folding carton productions are seeking to develop fiber-based alternatives to plastic packaging. One example is the KeelClipTM paper fastener replacing rings, tops and shrink wrap packaging. Pessarelli proudly declared, “This innovative high-volume product, developed by our customer Graphic Packaging International, really benefits from the Zerand technology.”
Interested folding carton producers are invited to find out more about BWP Zerand offering a real alternative to increase production and reduce cost.
Find Your Machine
BW Papersystems offers a wide selection of paper industry equipment with industry-leading technology.
Learn more about the BW Papersystems equipment and products offered.